The katana is one of the most respected weapons in history, showing off centuries of expert skill and deep cultural meaning. Whether you’re a martial artist, a collector, or a history lover, knowing how to judge a katana’s quality is what separates real treasures from simple copies. If you are buying your first sword or checking a cherished family piece, learning the signs of great craftsmanship takes both careful observation and a real love for the old methods.
Genuine Japanese swords are not just tools for battle; they are living histories that hold the spirit of the maker. Every real blade speaks through the make-up of the steel, the waves of the forge, and the careful finishing touches. The gap between a first-rate katana and a factory-made knock-off is in recognizing these old, delicate qualities.
This guide will take you step by step through how to assess a katana. We’ll cover everything from first looks to the tiny details that single out superb swords. With practice in these methods, you will learn to admire and identify truly outstanding examples of this ancient art.
Visual Inspection: Reading the Blade’s Story
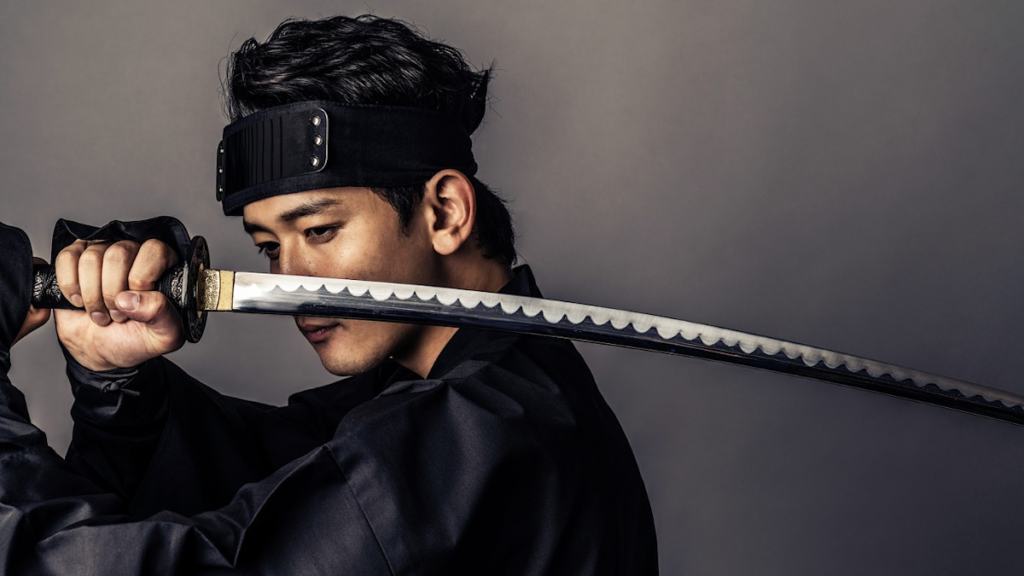
The first glance gives you the most telling clues about the sword’s quality. Start with the overall shape, especially the sori, or the blade’s curvature. A genuine katana shows a soft, flowing arc from the tang to the gently pointed tip. Knock-off blades, however, usually present sharp bends or uneven curves that shout out the use of machines instead of skilled hands.
Next, check for the hamon, the wavy, light-coloured line that runs close to the edge. This line is the result of differential hardening, where the blade was heated and quenched in a way that left the edge hard and the spine soft. Real hamon moves in a lively, irregular way, changing width and brightness along its length. Any version that looks too straight or too even—like a line drawn with a ruler—is simply machine-etched steel.
The blade’s surface finish is your third checkpoint. Japanese sword polishers, or togishi, spend months working with an ever-finer set of water stones. The end result is a glassy finish that not only glitter but lets you peer into the steel’s inner layers. What you want to see is hada, the fine, flowing patterns that resemble the grain in wood. These patterns prove the smith folded the steel and hammered it just right, a process that not only strengthens the blade but also reveals the soul of the metal.
Material Analysis: Unpacking Steel Brilliance
Every truly great katana starts with the metal and the skill used to shape it. Japanese swordmakers centuries ago perfected steel crafting by using highly controlled methods and the legendary folding process. By folding metal over and over—sometimes a few hundred times—they drew out tiny impurities and forged the beautiful, tiny whirls seen across a finished sword’s surface.
The best katana blades are usually made from tamahagane steel, created in small, traditional forges, or from modern high-carbon steels engineered to forge the same qualities. The exact carbon level is critical: too little yields a blade that bends and dulls, while too much creates a desperate brittleness. Through centuries of trial, the master smiths locked in that sweet spot.
Look closely for welding seams and joints, especially in blades made from different steels. In a kobuse sword, the razor-sharp edge is hard steel married to a softer spine for shock resistance. If the join wasn’t perfect, you’ll see rough, ugly seams, mismatched colors, or tiny gaps. Good-forging will hide all that, because great craftsmanship never advertizes itself.
Craftsmanship Details: Beyond the Blade
Look closely at the tsuka (handle) and you’ll see the sword’s true quality. A genuine katana has a full-tang blade—the steel runs straight through the tsuka and stays tight with mekugi (bamboo pegs). The whole handle feels solid and perfectly balanced, and the ito (cord) wrapping, made of real silk or cotton, follows classic patterns layered over same (ray skin).
Next, examine the tsuba (hand guard). Good tsubas show expert skill: clean, straight lines, the right thickness, and a fit that won’t loosen or jiggle when you’re swinging the sword. The guard should fit tightly against the blade. Many tsubas carry traditional patterns or family crests that tell a story of Japanese culture.
Finally, don’t overlook the saya (scabbard). A proper saya is made of wood and given several coats of lacquer, making the surface smooth and glossy. Inside, the blade should slide out easily but sit snugly with no rattling. A quality saya has a koiguchi (mouth) that’s been strengthened and comes with classic silk hanging fittings, ensuring that the whole sword is safe and quick to draw.
Historical Accuracy: Context and Provenance
When we talk about evaluating a katana, the time it was made can change everything, especially for older swords. Each era shaped the blade’s shape, proportion, and how it was made. Kamakura era swords (1185-1333) will feel and look different from the ones crafted during the Edo era (1603-1868). Learning these signs helps us separate real treasure from modern fakes that try too hard to look old.
When we can trace a blade’s journey, it adds a lot more value. Records showing which school made it, the smith’s signature (mei), and the names of past owners create a richer history for the blade. Still, be careful. Some sellers try to link a blade to famous names or long ago owners without real proof and without expert backing.
Always check the tang (nakago) for marks or signatures. Real mei are written in confident, flowing strokes that show a skilled hand. Fakes often have shaky, uneven strokes that don’t match the known work of the claimed smith. For high-value pieces, it’s wise to get a pro opinion.
Handling and Balance: The Test of True Quality
Balance is the unsung hero of a katana’s quality. A truly outstanding blade feels almost alive, and the sweet spot, called tachi-kaze, usually sits about 4 to 6 inches past the tsuba. When the balance is right, you can move the blade quickly and in control, whether you’re landing a deep cut or defending against a strike.
The blade should feel solid but quick in your hands, lighter at the guard than at the tip and never lagging at either end. Well-made swords balance themselves so that every arc of the cut comes naturally. Poorly made ones tip forcefully left or right, forcing the wrist into awkward corrections that lead to missed cuts and missed targets.
Treat the sword with the respect and safety it deserves. The grip must nestle securely into your palm, wrapped in material that keeps it steady even when hands sweat. Notice anything loose—vibrations, a tiny rattle, or gaps between parts—in the handle, guard, or pommel. Each sound is a warning that the structure is failing or the sword was never made to last.
Taking the last step in your judgment
Examining a Japanese blade takes time, experience, and a watchful eye that keeps all parts in view. The finest swords reveal a living balance: flawless steel, folded with skill; fittings shaped and inlaid with care; and a finish so smooth that the line between blade and handle seems to vanish.